Innovative method for carbon fibre recycling
Researchers from the Fraunhofer Institute for High-Speed Dynamics, Ernst-Mach-Institute, (EMI) have developed a technology that makes it possible to reclaim continuous carbon fibres from composite materials
Posted On 01 Apr 2025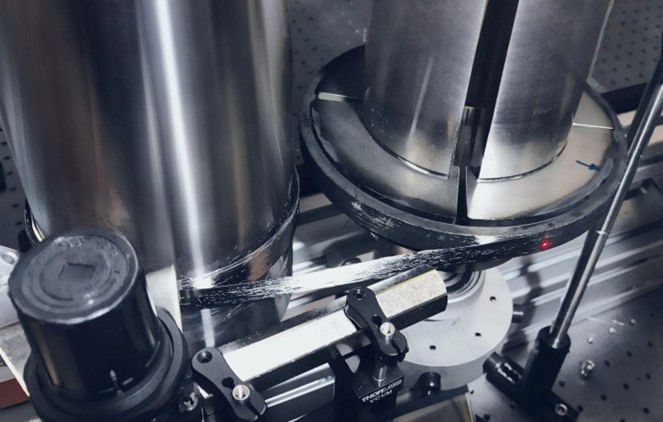
© Fraunhofer EMI. Experimental setup used for the local high-power laser-induced pyrolysis of a wound composite ring with simultaneous reclamation of the matrix-free carbon fibre roving. During the process, pyrolysis takes place at the position indicated
Researchers from the Fraunhofer Institute for High-Speed Dynamics, Ernst-Mach-Institute, (EMI) have developed a technology that makes it possible to reclaim continuous carbon fibres from composite materials — without diminishing material quality. High-power lasers are used for local degradation of the matrix of multi-layered fibre-reinforced plastics at high temperatures. This method offers not only ecological benefits but also considerable economic potential.
Carbon fibre composites are exceptionally strong and lightweight, making them preferred materials in many industries. But the disposal and recycling of these high-performance materials pose significant challenges. The research team at Fraunhofer EMI has now developed a process in which fibres from used composites are efficiently prepared for reuse — without adversely affecting their mechanical properties. Current recycling methods for fibre-reinforced plastic involve a shredding step, which shortens the fibres and leads to a downcycling.
Crash course in materials science: thermosetting vs. thermoplastic composites
A carbon fibre composite consists of yarns of fibres embedded in a polymer. This makes it possible to hold the fibres together, maintain the geometry of a component and protect the fibres from environmental influences. The fibres can be embedded in two kinds of plastic: Thermosetting composites consist of a matrix that cannot melt, meaning that they cannot be reprocessed, these behave like an adhesive that cures and then forms a durable bond. Thermoplastic composites, by contrast, can be melted and reprocessed. However, thermosetting plastics are easier to process, and are therefore used more frequently in industrial structural applications.
Peeling-based recycling of wound structures
The researchers at Fraunhofer EMI use a high-power laser for controlled reclamation of the fibre reinforcement from thermosetting composites. This method is especially relevant for pressurized hydrogen tanks, where a continuous carbon fibre roving is wound around a plastic liner to make the tank able to withstand high internal service pressures of up to 700 bar.
The advantage of this innovative recycling method lies in the ability to remove the thermosetting matrix surrounding the carbon fibres via a local pyrolysis, while leaving the fibres themselves nearly undamaged. »What makes this process special is that we perform the pyrolysis of the matrix and the unwinding of the fiber roving simultaneously, at a reasonable speed without damaging the carbon fibers«, explains project manager Mathieu Imbert.
The challenge lies in defining the optimum process window, as the matrix thermal degradation occurs at temperatures of 300 to 600 degrees Celsius, while the fibres might start getting damaged when the temperature reaches about 600 degrees Celsius. »We found a very good compromise between the process efficiency and the quality of the recycled material. Our results show that the continuous fibres reclaimed in this way have the same excellent performance properties as new fibres, which makes this method highly attractive«, Imbert says.
Economic and ecological advantages in one
The innovative method offers not only ecological benefits but also considerable economic potential for recycling companies. Because heat is applied locally and the fibre roving is continuously reclaimed at the same time, there is no need for the long pyrolysis times and high process costs typically required when working with the thick-walled hydrogen tanks. Furthermore, the laser-assisted reclamation process requires only about one-fifth of the amount of energy required to produce new fibres. Those are key advantages in the current context of rising energy costs and increasing environmental requirements. The project is slated to run until the end of 2025. It is part of the DigiTain project funded by the German Federal Ministry for Economic Affairs and Climate Action (BMWK). The researchers are currently working to make the process even more energy-efficient and to further improve the quality of the reclaimed fibres. The research team views the extremely positive link between the high quality of the recycled material and low process costs as the key argument in their plans to transfer the new method to the recycling industry.
Realted Content
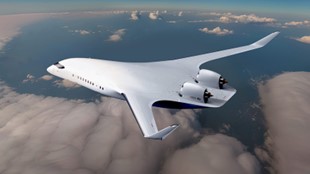
Siemens unveils breakthrough innovations in ind ...
Siemens showcased its vision for the ...
Read More