The EOLIAN project to develop recyclable wind turbine blades
The EOLIAN project is aiming to develop a new generation of blades manufactured using bio-based repairable and recyclable vitrimer composites reinforced with natural basalt fibres
Posted On 28 Mar 2025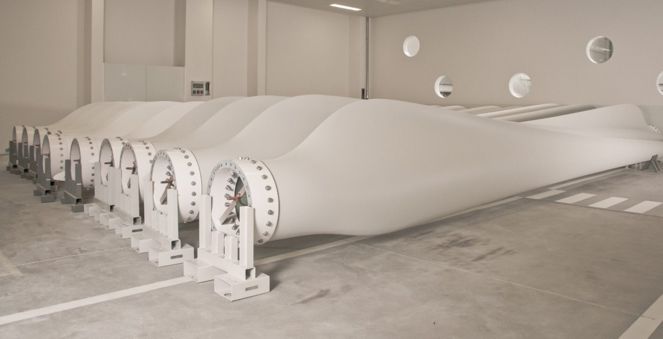
Turbine blades © Norvento.
A significant proportion of the installed wind turbines, the generation of the 2000s, will reach the end of their lifetime between 2020 and 2030. While 85-90% of a wind turbine’s total mass can be recycled, the rotor blades present a challenge, mainly due to their complex design and the composite materials used in their manufacture. Each MW of installed capacity corresponds to 12-15 tons of composites waste, which means that thousands of tons of blade waste will be accumulated not only in Europe, but also worldwide.
Wind turbine blades are currently manufactured out of a complex materials mixture mainly consisting of epoxy, vinyl ester or polyester resins reinforced with glass or/and carbon fibres, in combination with PVC and PET foams or balsa wood. Nowadays, the blade industry primarily uses glass fabric reinforced epoxy composites, and there are even some companies using carbon fibres for blades of larger dimensions.
Up to now, a suitable material to replace the E-glass fabrics and the epoxy resin in the composites solution for wind blades has not been found.
Additionally, there is currently no mature technique available for the recycling of such composite rotor blades: this combination makes it very difficult to split the materials and recycle the parts.
EOLIAN blades
The EOLIAN project, funded under European Union’s Horizon Europe research and innovation programme, is aiming to develop a new generation of blades manufactured using bio-based repairable and recyclable vitrimer composites reinforced with natural basalt fibres.
In EOLIAN’s Work Package 1 (Industrial requirements and specifications) industrial partners Norvento Enerxía and Zorlu Enerji will specify the requirements, in terms of materials and operation, so that the composites solution developed in the project can fulfil the wind industry’s requirements. Moreover, a detailed review of blade design and manufacturing standards will be carried out to define how materials, in the coupon and subcomponent level, should be tested and characterized.
The data and methodologies gathered at this stage of the project will serve as guidance for the partners on the composites development side, so that the materials created within the consortium can serve as a universal solution in the wind turbine blade industry.
Progress and next steps
Since the project’s kick-off (June 2024), Norvento Enerxía and Zorlu Enerji have gathered a detailed specification of the EOLIAN materials requirements for blade design and manufacturing. These parameters have been previously agreed with partners. With this information, they will try to tune the vitrimer resin’s properties and develop new composite materials which are in line with wind industry stakeholders.
In parallel, Norvento Enerxía will launch the design and manufacturing of two 14 m long wind turbine blades:
a traditional blade manufactured with glass fibre and epoxy resin;
a bio-based blade manufactured with basalt fibres or a hybrid solution of glass fibres with basalt fibres, and the vitrimer resin.
This will make it possible to evaluate the mechanical properties and overall performance of these new bio-based solutions.
These results will provide guidance to virtually design a third blade in which enhancements regarding the overall performance of the blade will be included. A classical LCOE (levelised cost of energy) analysis will be carried out to compare the three blade designs. The life cycle assessment (LCA) output from Work Package 7 (Sustainability analysis and risk assessment) will also be considered to evaluate which is an optimum design.
The blade design developed in EOLIAN will be used in Norvento’s nED100 wind turbine model.
Realted Content
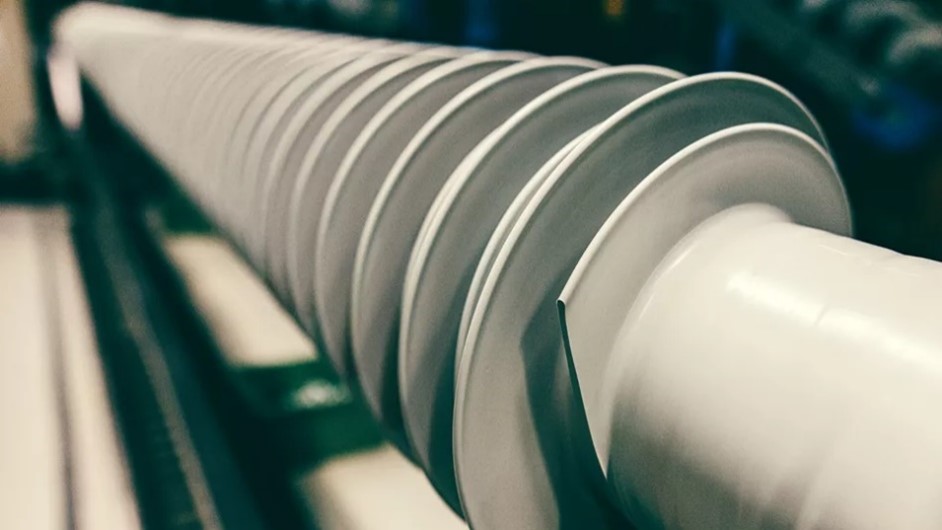
Hitachi Energy to increase production of critic ...
Hitachi Energy is expanding its trans ...
Read More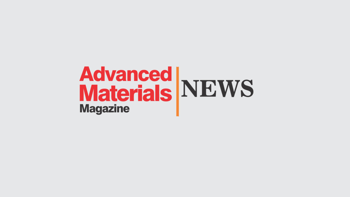
Pwnage unveils the carbon fibre composites mouse
Pwnage, a leader in premium gaming pe ...
Read More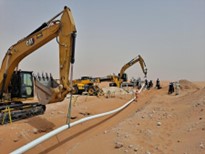
Strohm to supply Thermoplastic Composite Pipe f ...
Following a successful pilot with Ara ...
Read More